Comprehensive Service
- Index
- Comprehensive Service
Comprehensive Service
Help you to solve the hot runner problems?
- Could not find the service of your hot runner
- Can not find the spare parts for your hot runner
- Want to optimeze your hot runner
- Want total solution
We provide our professional and solutions?
- Many doctors are professional in hot runner system
- Over than 20 engineers have more than 10 years experience in hot runner
- Specializes in mold flow analysis
- Expert in thermal analysis
- Comprehensive e-learning system
- We service in Taiwan, Shanghai, Guangzhou, Chengdu, Xiamen, Hanoi, etc.
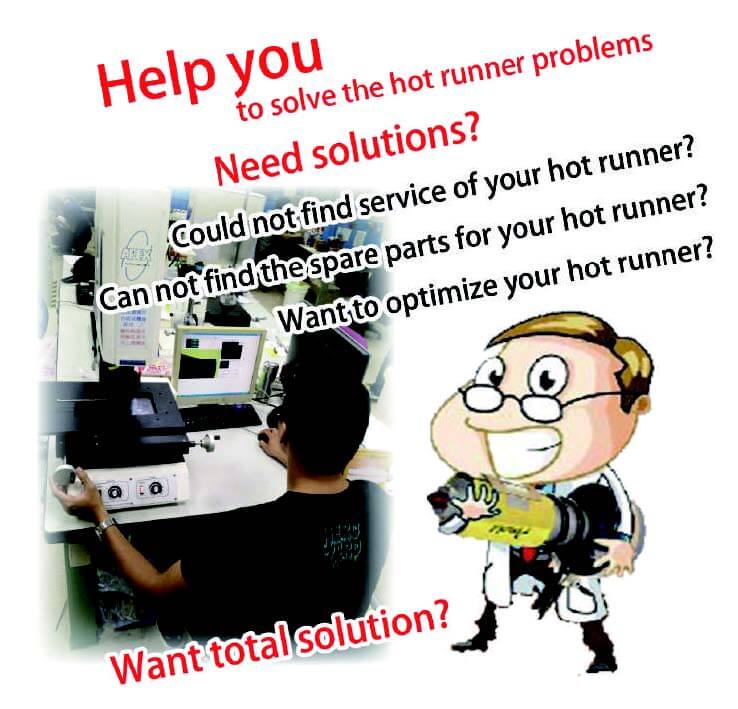